Carbon Dioxide Production Process: From Air to Industry
- acciomatespa
- Jan 28
- 3 min read
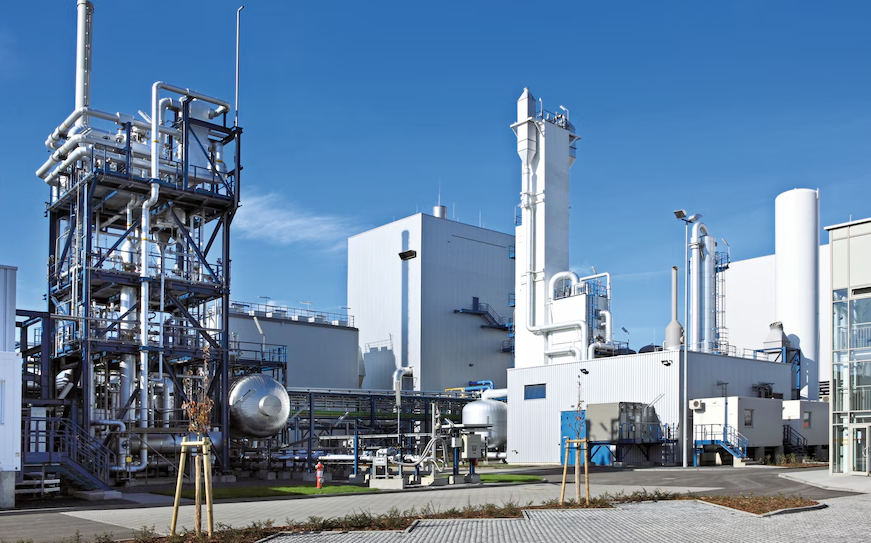
Carbon dioxide (CO₂) is a versatile and essential gas in various industries, from the production of carbonated beverages to its use in medical, agricultural and industrial applications. Although it is a naturally occurring gas in the environment, its industrial production follows a carefully designed process to ensure its purity, safety and efficacy. In this note, we will explore the fundamental stages of the carbon dioxide production process, highlighting its relevance for sustainable development and its impact on industrial innovation.
1. Sources of CO₂ Production
Carbon dioxide can be obtained from a variety of sources, depending on the needs of the industry and the local availability of raw materials. The main sources include:
Fermentation processes: Used in the production of alcohol and bioethanol, where CO₂ is a natural byproduct.
Ammonia plants: The ammonia production process generates large amounts of carbon dioxide as a byproduct.
Fossil fuel combustion: CO₂ is captured directly from exhaust gases in power plants or industrial processes.
Ambient air: In certain cases, direct air capture is used using advanced technologies.
The choice of source depends on the available infrastructure and the specifications of the CO₂ required.
2. Carbon Dioxide Capture
Once the source has been identified, CO₂ is captured using specific processes designed to maximize its recovery. These processes vary depending on the source:
Fermentation: The CO₂ released during fermentation is collected directly from the gas produced.
Flue gases: CO₂ is separated by technologies such as chemical absorption (using amines) or membrane processes.
Direct Air Capture: Uses advanced adsorbent materials that extract CO₂ from ambient air.
Efficient harvesting is essential to ensure a constant supply and reduce environmental impact.
3. Purification
Captured carbon dioxide may contain impurities such as water, oxygen, nitrogen, hydrocarbons or sulfur. These impurities must be removed to meet industrial and commercial standards. The purification process includes:
Dehydration: Removal of moisture using dryers or desiccants.
Pressure Sensitive Adsorption (PSA): To separate other waste gases.
Chemical filtration: To remove traces of unwanted compounds, such as sulfur or hydrocarbons.
The result is high purity CO₂, suitable for use in critical applications such as food, beverage and medical products.
4. Compression
Purified CO₂ is compressed to facilitate its transport and storage. Depending on the required state (liquid or gaseous), the CO₂ is subjected to different levels of pressure:
Gaseous CO₂: Compressed at pressures between 15 and 20 bars.
Liquid CO₂: Cooled and compressed at pressures above 50 bars, allowing it to be stored in liquid form at temperatures close to -20°C.
Efficient compression is crucial to optimizing transportation costs and ensuring safety.
5. Liquefaction (Optional)
For certain applications, such as long-distance transportation or bulk storage, CO₂ is liquefied through a controlled cooling process. This step converts the gas into a liquid that takes up less volume and makes it easier to handle.
Liquefaction plants are designed with advanced systems that minimize energy losses and improve operational efficiency.
6. Storage
Compressed or liquefied carbon dioxide is stored in specialized tanks designed to withstand high pressures and controlled temperatures. Storage types include:
Cryogenic tanks: For liquid CO₂, with thermal insulation that maintains low temperatures.
Steel cylinders: For gaseous CO₂ in smaller quantities.
Pressurized silos: For large volumes intended for industrial applications.
Proper storage is essential to preserve the quality of CO₂ and ensure safety during handling.
7. Transport
CO₂ is transported from production plants to customers using methods adapted to the quantity and distance:
Cryogenic tankers: For the transport of liquid CO₂.
Pressurized cylinders: For smaller quantities and local distribution.
Pipelines: In large-scale industrial applications, such as oil well injection or underground storage.
Each transportation method meets strict safety and efficiency regulations.
8. Final Applications
Industrially produced carbon dioxide has a wide range of applications, including:
Food and beverages: Carbonation of soft drinks, food preservation and modified atmospheres.
Agriculture: Fertilization in greenhouses to promote plant growth.
Chemical industry: Production of carbonates, urea and polymers.
Medicine: In applications such as laparoscopies and respiratory therapies.
Energy and Environment: Carbon Capture and Storage (CCS) to mitigate climate change.
Commitment to Sustainability
Carbon dioxide production is evolving towards more sustainable practices, with a focus on:
CO₂ Capture and Reuse (CCU): Transforming captured CO₂ into useful products such as synthetic fuels.
Emissions reduction: Use of efficient technologies to minimize the carbon footprint.
Circular economy: Recycling CO₂ in industrial processes to reduce the consumption of raw materials.
These initiatives reflect the industry's commitment to responsible and sustainable development.
Conclusion
The carbon dioxide production process is an example of how advanced engineering and technological innovation can transform a natural resource into an essential input for multiple industries. Each stage, from capture to distribution, is designed to ensure a high-quality, efficient and safe product.
At Acciomate Engineering & Projects , we offer engineering and project services that optimize each stage of this process, helping companies improve their competitiveness and sustainability.
Comments