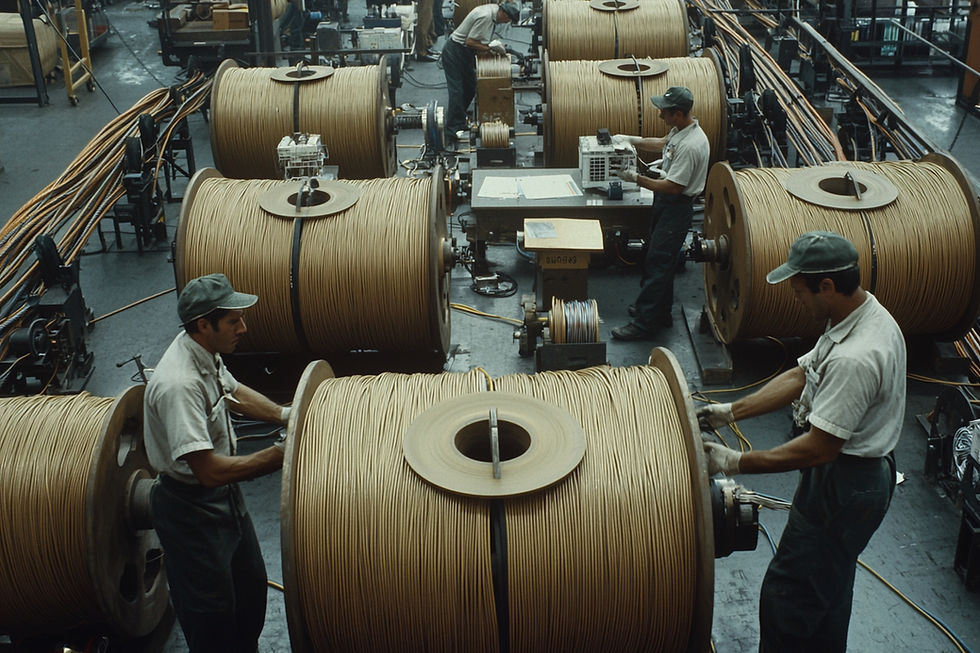
Copper is known as the “red metal” for its ductility, conductivity and strength, qualities that make it the preferred material for the manufacture of electrical cables. From its extraction in mines to its conversion into highly functional cables, the production process combines advanced technology, precision engineering and quality control. Each stage ensures that the cables meet the most demanding standards to guarantee their performance in electrical and industrial systems.
In this note, we will explore the fundamental stages of the copper cable production process, highlighting how each step contributes to a reliable, efficient and sustainable final product.
1. Copper Extraction and Refining
The copper cable production process begins with obtaining the mineral in its natural state:
Extraction:
Copper is extracted from open-pit or underground mines in the form of minerals such as chalcopyrite, bornite or malachite.
Concentration:
The extracted mineral is ground and subjected to flotation, a chemical process that separates the copper from the rest of the material.
Refinement:
A smelting furnace is used to obtain blister copper (97-99% purity). It is then electrorefined, reaching a purity of 99.99%, ideal for electrical applications.
2. Copper Rod Production
Refined copper is converted into rods, the base material for cable manufacturing:
Melting and casting:
Refined copper is melted in specialized furnaces and poured into molds to form bars or ingots.
Laminate:
The bars are processed in rolling mills where they are stretched and shaped to form copper rods with a uniform diameter, usually between 8 and 12 mm.
Quality control:
The rods are inspected to ensure they meet the required purity and strength standards.
3. Copper Stretching
At this stage, the copper rods are transformed into wires of smaller diameters:
Stretching machines:
The rods are passed through a series of dies that gradually reduce their diameter until they reach the desired size. This process improves the mechanical strength of the copper.
Annealing:
To restore copper's ductility after drawing, it is subjected to thermal annealing, making it more malleable and easier to manipulate.
Verification:
The resulting wire is tested to ensure uniformity and conductivity.
4. Cable Insulation
Drawn copper wire is coated with insulating materials to protect it from corrosion and ensure its safety in electrical applications:
Application of insulation:
The wire is coated by an extrusion process, using materials such as PVC, polyethylene or XLPE.
Thickness control:
During extrusion, the thickness of the insulation is monitored to comply with technical regulations.
Dielectric tests:
Insulating properties are checked to ensure that the cable can withstand the specified voltage levels.
5. Braiding and Setting
At this stage, several insulated wires are bundled or twisted together to form more complex cables:
Braided:
The wires are braided to improve their flexibility and mechanical strength, preventing breakage due to torsion.
Core formation:
In multicore cables, stranded wires are grouped together to form the core of the cable.
6. Exterior Coating
The core of the cable is covered with a protective sheath that isolates it from external factors:
Coating:
An extrusion process is used to apply an outer layer of materials that are resistant to abrasion, moisture, chemicals and high temperatures.
ID:
Cables are marked with information such as type, voltage, material and manufacturer.
7. Testing and Quality Control
Before being marketed, the cables undergo rigorous quality tests:
Conductivity tests:
It is ensured that copper meets electrical efficiency standards.
Mechanical tests:
They include tensile, flexural and abrasion resistance.
Electrical tests:
Dielectric strength, insulation capacity and fire resistance are checked.
8. Packaging and Distribution
The finished cable is packaged for transport and distribution:
Rolled:
Cables are wound onto coils or reels for easy handling and storage.
Protection:
They are packed with materials that protect them from damage during transport.
Labeled:
Each reel includes technical specifications and traceability details.
Benefits of an Efficient Process
Quality Guaranteed: Every stage of the process ensures a final product that meets international standards.
Sustainability: Many copper wire factories are adopting environmentally friendly practices such as copper recycling and efficient energy use.
Versatility: Copper cables are suitable for a wide range of applications, from residential electrical installations to high-capacity industrial systems.
Conclusion
The copper cable production process is an example of how technology, precision and quality control combine to create products essential to the global electrical infrastructure. Every stage, from copper extraction to final packaging, is designed to ensure maximum efficiency, durability and performance.
At Acciomate Engineering & Projects , we offer customized solutions to optimize industrial production processes, guaranteeing quality, efficiency and sustainability in each project.
Comments